Silicone Parts and Seals
Diyak Rubber has created silicone parts and seals for a broad range of industries including medical, automotive, aerospace, electronics and more. From simple seals to the most complex silicone parts, we utilize a host of sophisticated technologies and processes to consistently manufacture the high-quality silicone components your applications demand.
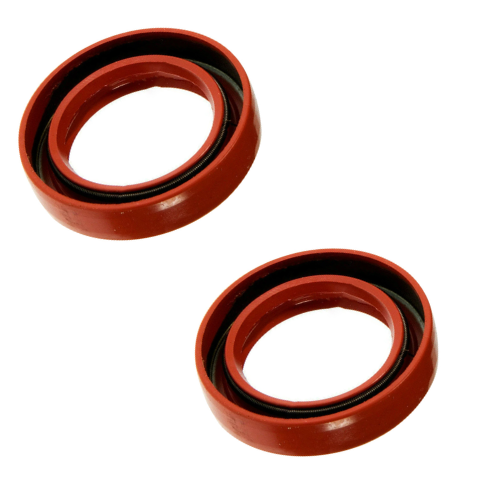
Types of Silicone
Silicone
- Trade Names
- Silplus — Momentive Performance Materials
- Silbione — Elkem
- Xiameter— Dow
- Elastosil — Wacker
- Shin-Etsu KE — Shin-Etsu
- ASTM D1418 Designation
- MQ, PMQ, VMQ, PVMQ
- ASTM D2000/SAE J200 Type, Class
- FC, FE, GE
- Diyak Compound Designation
- SL
- Standard Color
- Red
- Description
- A group of elastomers, made from silicon, oxygen, hydrogen and carbon, Silicones are renowned for their retention of flexibility and low compression set characteristics, within one of the widest working temperature ranges for elastomers.
- Key Uses
- Static seals in extreme temperature situations.
- Seals for medical devices, compatible with FDA regulations.
- Low outgassing and excellent dampening properties.
- Temperature Range
- Standard Compound: -85°F to +400°F
- Special Compounds: -148°F to +400°F
- Hardness (Shore A)
- 5 to 80
- Features
- Phenyl (PVMQ) based silicones can perform to -148°F.
- Metal fillers and conductive carbon black make silicone conductive for EMF/RF applications.
Silicone
- Trade Names
- Silplus — Momentive Performance Materials
- Silbione — Elkem
- Xiameter— Dow
- Elastosil — Wacker
- Shin-Etsu KE — Shin-Etsu
- ASTM D1418 Designation
- MQ, PMQ, VMQ, PVMQ
- ASTM D2000/SAE J200 Type, Class
- FC, FE, GE
- Diyak Compound Designation
- SL
- Standard Color
- Red
- Description
- A group of elastomers, made from silicon, oxygen, hydrogen and carbon, Silicones are renowned for their retention of flexibility and low compression set characteristics, within one of the widest working temperature ranges for elastomers.
- Key Uses
- Static seals in extreme temperature situations.
- Seals for medical devices, compatible with FDA regulations.
- Low outgassing and excellent dampening properties.
- Temperature Range
- Standard Compound: -85°F to +400°F
- Special Compounds: -148°F to +400°F
- Hardness (Shore A)
- 5 to 80
- Features
- Phenyl (PVMQ) based silicones can perform to -148°F.
- Metal fillers and conductive carbon black make silicone conductive for EMF/RF applications.
Fluorosilicone
- Trade Names
- FE — Shin-Etsu
- Elastosil— Wacker
- Silastic LS — Dow
- FSE — General Electric
- ASTM D1418 Designation
- FVMQ
- ASTM D2000/SAE J200 Type, Class
- FK
- Apple Compound Designation
- FS
- Standard Color
- Blue
- Description
- Fluorosilicone combines the good high and low temperature stability of Silicones with the fuel, oil, and solvent resistance of Fluorocarbons.
- Key Use(s)
- Aerospace fuel systems. Auto fuel emission control systems. Primarily for static sealing and low outgassing applications.
- Temperature Range:
- Standard Compound: -75°F to +400°F.
- Hardness (Shore A)
- 40 to 80.
- Features
- Fluorosilicone is most often used in aerospace applications for systems requiring fuel and/or diester-based lubricant resistance up to 400°F.
- Although generally specified for aerospace use, due to its excellent fuel resistance and high temperature stability, Fluorosilicone is becoming an increasingly popular material for a wider range of sealing applications.
- Featuring good compression set and resilience properties, fluorosilicone compounds are suitable for exposure to air, sunlight, ozone, chlorinated and aromatic hydrocarbons.
- Limitations
- Due to limited physical strength, poor abrasion resistance, and high friction characteristics, Fluorosilicone elastomers are not generally recommended for dynamic sealing. They are predominantly designed for static sealing use. They are also not recommended for exposure to brake fluids, hydrazine, or ketones.
Liquid Silicone Rubber
LSR is a low viscosity silicone elastomer intended for use in liquid injection molding (LIM) equipment. It offers high thermal stability and flexibility at low temperatures, high transparency and is easily colored. Also, self-lubricated and electrically conductive grades are available as well as FDA and medical compliant grades. Liquid silicone rubber is widely used to mold complex profiles because of its excellent flow characteristics. See Silicone for other key benefits.
Silicone comes in many forms. Compression, transfer and rubber injection use High Consistency (HC) silicone. LSR silicones are injection molded.
Liquid Silicone Rubber
Liquid silicone rubber (LSR) and silicone rubber are extraordinary manufactured materials. By combining the appropriate additives, in the correct amounts, silicone is transformed into a highly specific material.
- It can insulate, or be conductive
- Silicone can withstand freezing temperatures and stand up to high heat
- It can be translucent as well as almost any color, even glow-in-the-dark green
- Silicone resists fungus and at the same time, it is non-toxic
From the cleanroom to the operating room, from the dashboard to the circuit board, silicone rubber exhibits such a wide range of properties, it is used in many applications where organic rubber cannot perform.
State-of-the-Art Molding Capabilities
The popularity of silicone has led to DiyakRubber’s development of precision mold capabilities. Even the most complex silicone parts and seals can be consistently manufactured using a host of technologies and processes including injection molding and compression molding.
We give you all the advantages of silicone… and then some.
- Unmatched temperature resistance: withstands temperature extremes from -155°F to 400°F
- Excellent mechanical properties: good elongation, excellent flexibility and a durometer range of 10-80 Shore A
- Superior insulating properties
- Exceptional weather resistance: resists the damaging effects of UV light, ozone, O2, weather, moisture and steam with outstanding aging characteristics
- Good chemical resistance: resists water and many chemicals such as some acids, oxidizing chemicals, ammonia and isopropyl alcohol. Note: concentrated acids, alkalines and solvents should not be used with silicone rubber
- Excellent dimensional stability: offers excellent accuracy and provides versatility of shape and form to many seals and parts, even intricate shapes