The Importance of Bonded Parts in Rubber Seals and Gaskets
Bonded parts are a cornerstone of many industries that rely on durable and precise sealing solutions. These components combine the flexibility of rubber with the strength of metal or other rigid materials, resulting in a hybrid product designed to perform under demanding conditions.
In this article, we will explore the features, benefits, applications, and materials used in bonded parts, highlighting their significance in industrial and commercial applications.
What Are Bonded Parts?
Bonded parts refer to components where rubber or elastomeric material is chemically or mechanically bonded to a rigid substrate, such as metal, plastic, or fabric. This bonding process creates a single, unified part that combines the unique properties of both materials.
Typical examples of bonded parts include rubber-to-metal bonded seals, vibration dampers, and gaskets.
Key Features of Bonded Parts
1. Enhanced Durability: Bonded parts are designed to withstand extreme conditions, including high pressure, temperature fluctuations, and mechanical stress.
2. Precise Sealing: The seamless integration of rubber and metal ensures excellent sealing capabilities, even in complex environments.
3. Versatility: Available in a variety of shapes, sizes, and material combinations, bonded parts can be tailored to suit specific applications.
4. Corrosion Resistance: The use of treated metals and robust elastomers ensures that bonded parts remain unaffected by corrosion over time.
5. Cost-Efficiency: By combining multiple materials into a single component, bonded parts reduce assembly complexity and enhance product lifespan.
The Manufacturing Process of Bonded Parts
The production of bonded parts typically involves the following steps:
1. Surface Preparation
The substrate, such as metal, is cleaned and treated with an adhesive to ensure proper bonding.
2. Rubber Molding
The rubber material is molded to the desired shape, ensuring precision and consistency.
3. Curing Process
The assembly undergoes a curing process to establish a strong bond between the rubber and substrate.
4. Quality Testing
Each bonded part is tested for durability, adhesion strength, and performance under specified conditions.
Applications of Bonded Parts
Bonded parts are essential in various industries due to their reliability and adaptability.
1. Automotive Industry
- Engine Mounts: Reduce vibration and noise in vehicles.
- Seals and Gaskets: Provide airtight and watertight sealing in engines and transmissions.
2. Aerospace Industry
- Used in hydraulic systems and fuel tanks for reliable sealing.
3. Oil and Gas Industry
- Employed in drilling equipment and pipelines to withstand extreme pressure and corrosive environments.
4. Industrial Machinery
- Act as vibration dampers and shock absorbers to protect machinery from wear and tear.
5. Medical Equipment
- Used in devices requiring precision sealing and biocompatibility.
Advantages of Bonded Parts Over Traditional Components
Feature Bonded Parts Traditional Components
Durability High Moderate
Sealing Efficiency Excellent Limited
Customization Highly Customizable Limited
Corrosion Resistance High Dependent on Material
Cost-Effectiveness Long-Term Savings Higher Maintenance Costs
Materials Used in Bonded Parts
1. Rubber Types
- EPDM (Ethylene Propylene Diene Monomer): Excellent for weather resistance and water sealing.
- Nitrile Rubber (Buna-N): Ideal for oil and fuel resistance.
- Silicone: Suitable for high-temperature applications.
- Viton (FKM): Provides superior chemical resistance.
2. Metal Substrates
- Steel: For high-strength and load-bearing applications.
- Aluminum: Lightweight and corrosion-resistant.
- Stainless Steel: Ideal for environments requiring superior corrosion resistance.
3. Plastic and Fabric Substrates
- Used for lightweight and flexible bonded components in less demanding applications.
Maintenance Tips for Bonded Parts
1. Regular Inspection: Check for signs of wear, deformation, or detachment between the bonded materials.
2. Avoid Overloading: Ensure bonded parts are used within their specified load and pressure limits.
3. Proper Cleaning: Use compatible cleaning agents to avoid damage to the rubber or metal surfaces.
4. Timely Replacement: Replace bonded parts showing significant wear to prevent system failure.
Why Choose Rubber Seals and Gaskets for Bonded Parts?
At Rubber Seals and Gaskets, we specialize in producing high-quality bonded parts tailored to meet the specific needs of various industries.
Our Strengths:
- Premium Materials: We use only the best rubber and substrate materials to ensure reliability.
- Expert Craftsmanship: Precision-engineered bonded parts for optimal performance.
- Custom Solutions: Tailored designs to match your unique requirements.
- Quality Assurance: Rigorous testing to guarantee durability and efficiency.
Conclusion
Bonded parts are the ideal solution for industries seeking reliable sealing, durability, and cost efficiency. Their unique construction combines the flexibility of rubber with the strength of rigid substrates, making them indispensable for a wide range of applications.
At Rubber Seals and Gaskets, we provide expertly crafted bonded parts that meet the highest standards of quality and performance. Contact us today to learn more about our range of products and how they can benefit your operations.
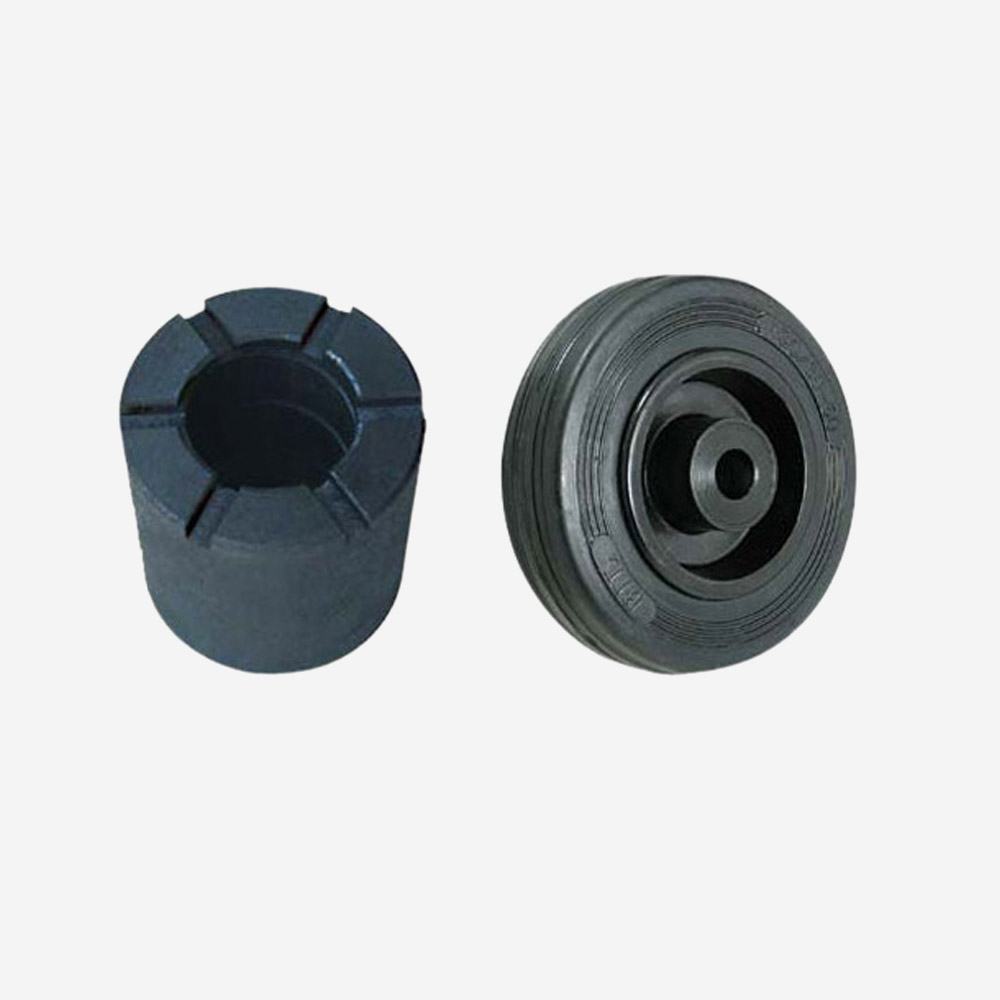
FAQs
Bonded parts are used in applications requiring reliable sealing, vibration damping, and durability under extreme conditions.
Bonded parts are made by chemically or mechanically bonding rubber to a rigid substrate like metal or plastic during a molding and curing process.
Yes, bonded parts can be customized in terms of material, size, and shape to meet specific application requirements.
For superior bonded parts, trust Rubber Seals and Gaskets – your partner in reliable sealing solutions!