Composite Bonding: Revolutionizing Sealing Solutions for Rubber Seals and Gaskets
In the world of industrial applications, the efficiency and durability of seals and gaskets are paramount. One of the most innovative methods to enhance these qualities is composite bonding, a process that combines multiple materials to create a superior, high-performance solution. At Rubber Seals and Gaskets, we leverage composite bonding technology to deliver products that meet the rigorous demands of modern industries.
This blog explores the concept of composite bonding, its benefits, materials used, applications, and why it is a game-changer for rubber seals and gaskets.
What Is Composite Bonding?
Composite bonding is a manufacturing technique where two or more materials are joined to create a single, integrated component. This process allows for the combination of materials with different properties, resulting in a product with enhanced performance characteristics, such as strength, flexibility, durability, and resistance to various environmental factors.
In the context of rubber seals and gaskets, composite bonding often involves bonding rubber with metals, plastics, or fabrics to achieve specific operational requirements.
Benefits of Composite Bonding
Composite bonding offers a wide range of advantages, making it a preferred choice for various sealing and gasket applications:
1. Enhanced Strength and Durability
By combining materials with complementary properties, composite bonded seals and gaskets exhibit superior tensile strength and longevity.
2. Improved Resistance to Environmental Factors
Composite bonding enhances resistance to chemicals, temperature extremes, and UV exposure, ensuring reliable performance in harsh conditions.
3. Customization
The process allows for the creation of tailored solutions to meet unique industrial requirements.
4. Lightweight Construction
Composite materials often weigh less than traditional options, reducing the overall weight of machinery or systems.
5. Cost Efficiency
While the initial manufacturing process may be more complex, the extended lifespan and reduced maintenance needs of composite-bonded components translate to long-term cost savings.
Materials Used in Composite Bonding
The choice of materials is critical to the success of composite bonding. Here are some commonly used materials:
1. Elastomers (Rubber)
- Examples: EPDM, Nitrile (Buna-N), Silicone, Viton (FKM)
- Purpose: Provides flexibility, sealing, and resistance to various environmental factors.
2. Metals
- Examples: Steel, Aluminum, Brass
- Purpose: Adds structural strength and rigidity to the bonded product.
3. Plastics
- Examples: PTFE, Nylon, Polyurethane
- Purpose: Offers lightweight construction and resistance to chemicals.
4. Fabrics
- Examples: Reinforced fabrics, Kevlar, Fiberglass
- Purpose: Enhances tensile strength and wear resistance.
5. Adhesives
- Examples: Epoxy, Urethane-based adhesives
- Purpose: Ensures a strong and durable bond between materials.
Applications of Composite Bonding in Rubber Seals and Gaskets
Composite bonding is employed in a variety of industries and applications:
1. Automotive
- Used in engine seals, gaskets, and vibration dampers to improve performance and longevity.
2. Oil and Gas
- Ensures reliable sealing in high-pressure and high-temperature environments.
3. Aerospace
- Lightweight and durable bonded components help reduce weight while maintaining performance.
4. Medical Devices
- Provides hygienic and biocompatible sealing solutions for critical medical equipment.
5. Industrial Equipment
- Used in pumps, valves, and compressors for superior sealing under demanding conditions.
How Composite Bonding Enhances Rubber Seals and Gaskets
Composite bonding transforms traditional rubber seals and gaskets into high-performance components by:
- Minimizing Wear and Tear
- The bonded layers reduce friction and extend the lifespan of the seal or gasket.
- Increasing Pressure Resistance
- Metal or fabric reinforcements enhance the ability to withstand high pressures.
- Improving Thermal Stability
- Materials like PTFE or metals improve temperature tolerance.
- Achieving Precise Fit
- Custom bonding processes ensure a perfect fit for specific applications.
Maintenance Tips for Composite-Bonded Products
To maximize the lifespan of composite-bonded seals and gaskets, follow these maintenance tips:
- Regular Inspections: Check for signs of wear, delamination, or damage.
- Proper Cleaning: Use suitable cleaning agents to remove dirt and debris.
- Correct Installation: Ensure proper alignment and avoid over-tightening.
- Storage Conditions: Store in a cool, dry environment away from direct sunlight.
Why Choose Rubber Seals and Gaskets for Composite Bonded Products?
At Rubber Seals and Gaskets, we specialize in delivering high-quality composite-bonded seals and gaskets tailored to your industry needs. Here’s why you should partner with us:
- Advanced Manufacturing: Cutting-edge composite bonding techniques ensure top-notch quality.
- Custom Solutions: We design products to meet your specific operational requirements.
- Expert Support: Our team offers guidance on material selection and product maintenance.
- Sustainability: Eco-friendly manufacturing processes that minimize waste.
Conclusion
Composite bonding has revolutionized the sealing industry, providing enhanced performance, durability, and customization for rubber seals and gaskets. Whether you’re in the automotive, aerospace, or oil and gas industry, composite-bonded solutions can significantly improve your operations’ efficiency and reliability.
Explore our range of composite-bonded products at Rubber Seals and Gaskets to find the perfect sealing solution for your application. Contact us today to learn more and take your sealing technology to the next level!
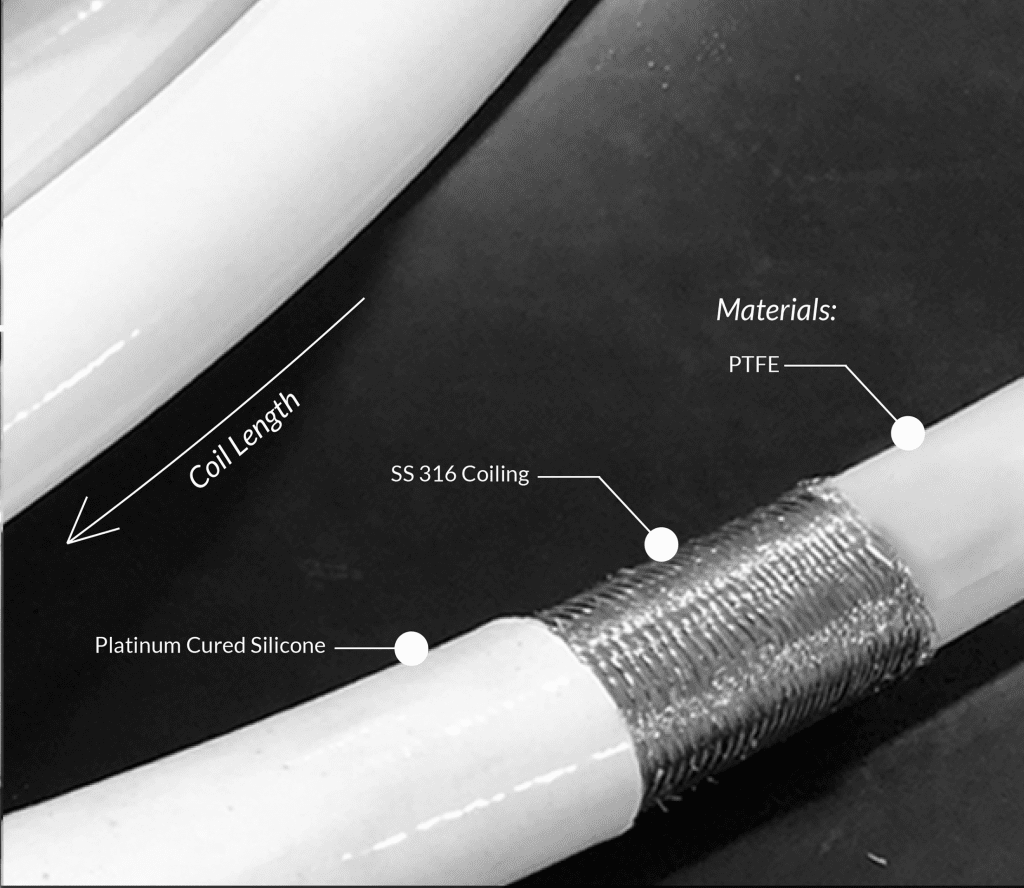
FAQs
The lifespan depends on the materials used and operating conditions, but composite-bonded gaskets generally last longer than traditional options.
Yes, composite bonding allows for custom designs to fit unique applications.
Consider factors like temperature, pressure, and chemical exposure. Our experts can help you choose the best materials.
For reliable and high-performance sealing solutions, trust Rubber Seals and Gaskets—where innovation meets quality!