Plastic Bonded Rubber Parts: The Perfect Blend for Enhanced Performance
In the world of sealing and gasket solutions, plastic bonded rubber parts are gaining immense popularity due to their exceptional durability, flexibility, and resistance to harsh environmental conditions. By combining the best properties of plastic and rubber, these components provide superior sealing, shock absorption, and insulation, making them ideal for various industrial applications.
In this blog, we will explore the benefits, applications, manufacturing process, and key considerations of plastic bonded rubber parts to help you understand why they are a preferred choice in industries like automotive, aerospace, construction, and more.
What Are Plastic Bonded Rubber Parts?
Plastic bonded rubber parts are composite components where rubber is securely bonded to a plastic substrate. This combination enhances the mechanical strength of the product while retaining the flexibility and sealing capabilities of rubber. These parts are widely used in applications requiring impact resistance, noise dampening, and weatherproofing.
The bonding process ensures a permanent adhesion between rubber and plastic, preventing separation even under extreme conditions. This makes plastic bonded rubber parts an essential solution in high-performance applications.
Advantages of Plastic Bonded Rubber Parts
1. Enhanced Durability
- The combination of plastic and rubber increases the overall lifespan of the component.
- Resistant to wear and tear, making them suitable for heavy-duty applications.
2. Excellent Sealing Properties
- Ideal for applications where airtight and watertight seals are required.
- Prevents leakage in mechanical and hydraulic systems.
3. Superior Shock Absorption
- The rubber component absorbs vibrations and shocks, reducing noise and impact damage.
4. Lightweight Construction
- Plastic is lighter than metal, reducing the overall weight of the final product.
- This is especially beneficial in the automotive and aerospace industries for fuel efficiency.
5. Chemical and Temperature Resistance
- Plastic bonded rubber parts can withstand harsh chemicals, oils, and extreme temperatures.
- Suitable for applications in industrial environments exposed to corrosive substances.
6. Cost-Effective Solution
- The combination of plastic and rubber reduces material costs compared to metal alternatives.
- Requires minimal maintenance and has a longer lifespan, leading to cost savings.
Applications of Plastic Bonded Rubber Parts
1. Automotive Industry
- Door seals, engine mounts, and suspension bushings.
- Improves vehicle noise reduction and overall performance.
2. Aerospace Industry
- Sealing components for aircraft doors and windows.
- Ensures high resistance to temperature fluctuations and pressure changes.
3. Industrial Machinery
- Used in gaskets, shock absorbers, and conveyor belt components.
- Enhances the durability and efficiency of machines.
4. Construction Industry
- Weatherproof seals for doors and windows.
- Provides insulation and reduces energy consumption.
5. Medical Equipment
- Used in sterilized sealing solutions for medical devices.
- Ensures hygiene and durability in medical applications.
Manufacturing Process of Plastic Bonded Rubber Parts
The manufacturing process involves advanced techniques to ensure a strong bond between plastic and rubber:
1. Surface Preparation
- The plastic surface is cleaned and treated to enhance adhesion.
- Common treatments include plasma treatment, chemical etching, or flame treatment.
2. Rubber Molding
- The rubber is molded into the desired shape through compression, injection, or transfer molding.
3. Bonding Process
- A bonding agent or adhesive is applied to the plastic component.
- The rubber is then cured to create a secure, permanent bond.
4. Quality Inspection
- Each component undergoes rigorous testing to ensure durability, flexibility, and bonding strength.
Choosing the Right Plastic Bonded Rubber Parts
When selecting plastic bonded rubber parts, consider the following:
1. Material Compatibility
- Ensure the rubber and plastic materials used are suitable for the intended application.
- Common materials include EPDM, silicone, nitrile rubber, and thermoplastics.
2. Environmental Conditions
- Consider exposure to chemicals, UV radiation, moisture, and extreme temperatures.
3. Load and Stress Requirements
- Choose components that can withstand mechanical stress and impact.
4. Compliance with Industry Standards
- Ensure the product meets regulatory and safety standards for your industry.
Why Choose Rubber Seals and Gaskets for Plastic Bonded Rubber Parts?
At Rubber Seals and Gaskets, we specialize in manufacturing high-quality plastic bonded rubber parts customized for various industries. Here’s why you should choose us:
✔ High-Quality Materials – We use premium-grade plastic and rubber for maximum durability.
✔ Custom Solutions – Tailored designs to meet specific requirements.
✔ Advanced Manufacturing Techniques – Precision-engineered components for superior performance.
✔ Strict Quality Control – Every product undergoes rigorous testing to ensure reliability.
✔ Expert Guidance – Our team assists you in selecting the best materials and designs for your needs.
Conclusion
Plastic bonded rubber parts provide a superior alternative to traditional sealing and cushioning solutions by offering durability, flexibility, and cost-effectiveness. Their ability to withstand extreme conditions while providing excellent sealing and shock absorption makes them indispensable in multiple industries.
Looking for customized plastic bonded rubber parts? Contact Rubber Seals and Gaskets today for premium-quality solutions tailored to your requirements!
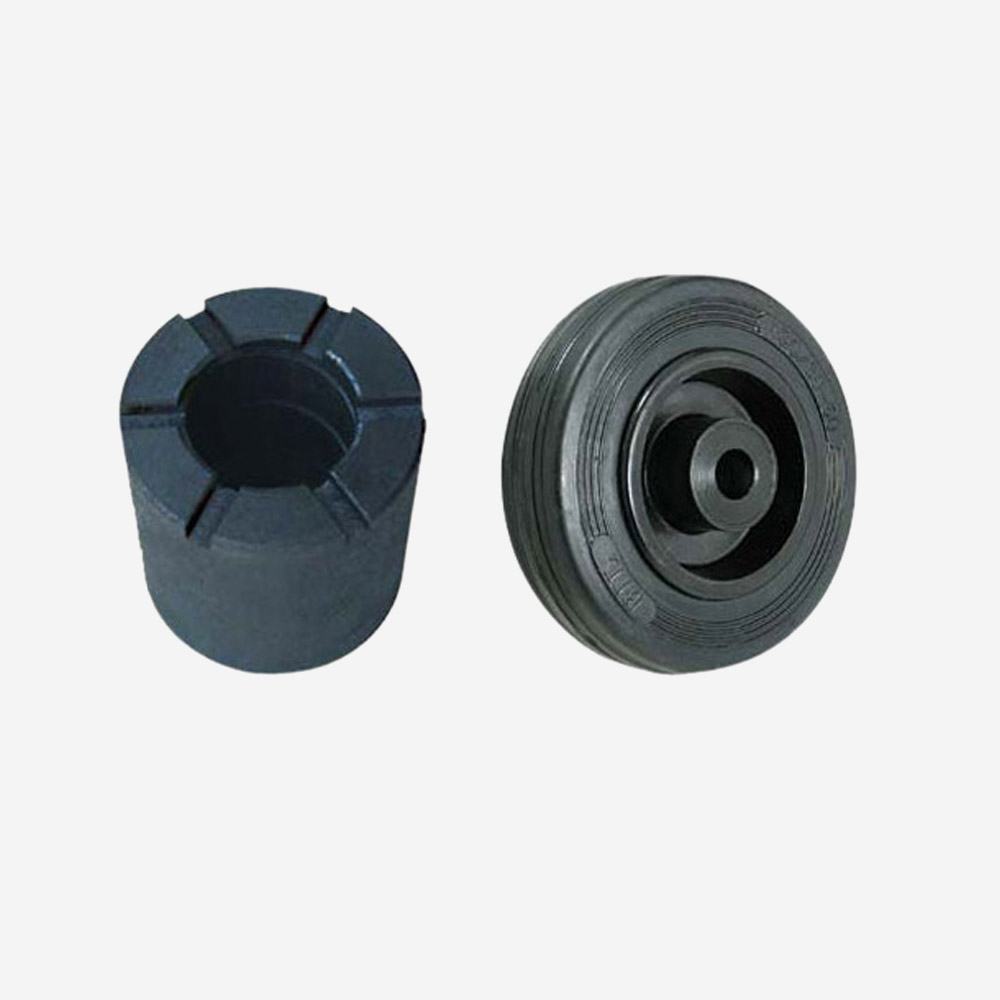
FAQs
EPDM, silicone, nitrile rubber, and thermoplastics like ABS and polycarbonate are commonly used.
Yes, they are designed to withstand high and low temperatures, depending on the material used.
Absolutely! At Rubber Seals and Gaskets, we offer tailored solutions for different industries.
Enhance your product’s performance with plastic bonded rubber parts from Rubber Seals and Gaskets! Contact us today for more information.