A Comprehensive Guide to Ring Joint Gaskets: Everything You Need to Know
When it comes to industrial sealing solutions, Ring Joint Gaskets (RJG) stand out for their durability, reliability, and ability to withstand extreme conditions. These gaskets are widely used in industries such as oil and gas, petrochemicals, and power generation, where sealing efficiency is critical. In this article, we’ll delve into the world of Ring Joint Gaskets, exploring their design, materials, applications, and advantages.
What Are Ring Joint Gaskets?
Ring Joint Gaskets are precision-engineered metallic sealing solutions designed for high-pressure and high-temperature applications. They are commonly used in flange connections to create a leak-proof seal, especially in pipelines transporting hazardous or volatile substances.
Unlike other types of gaskets, RJGs are metallic, making them highly resistant to deformation under extreme pressure. They are often oval or octagonal in shape, depending on the specific application and flange type.
Key Features of Ring Joint Gaskets
- High Pressure and Temperature Resistance
RJGs are ideal for applications involving pressures exceeding 15,000 psi and temperatures up to 1000°C, depending on the material used. - Reusability
In certain applications, these gaskets can be reused after proper inspection, making them cost-effective over time. - Precision Design
The precise machining of RJGs ensures a tight seal, reducing the risk of leaks even in challenging environments. - Material Versatility
These gaskets are available in a range of materials, including soft iron, stainless steel, Inconel, and more, allowing customization based on operational needs.
Common Materials for Ring Joint Gaskets
The choice of material significantly impacts the gasket’s performance and durability. Commonly used materials include:
• Soft Iron: Cost-effective and suitable for moderate pressure and temperature.
• Stainless Steel: Resistant to corrosion and suitable for harsh environments.
• Inconel: Offers excellent resistance to extreme temperatures and corrosive media.
• Hastelloy: Ideal for highly corrosive chemical applications.
• Low-Carbon Steel: Provides good sealing properties at a reasonable cost.
Each material is carefully selected based on compatibility with the flange material and the media being transported.
Applications of Ring Joint Gaskets
Ring Joint Gaskets are indispensable in various industries due to their robust sealing capabilities. Some notable applications include:
- Oil and Gas Industry
Used in pipelines, valves, and refineries to prevent leakage of hydrocarbons under high pressure. - Petrochemical Plants
Ensures the safe transportation of corrosive chemicals and volatile substances. - Power Generation
Commonly used in steam turbines, heat exchangers, and other equipment operating at high temperatures. - Aerospace and Defense
Ideal for critical sealing requirements in jet engines and other high-performance systems. - Marine Applications
Ensures secure sealing in shipbuilding and offshore drilling platforms.
Advantages of Using Ring Joint Gaskets
- Leak-Proof Sealing
RJGs provide unmatched sealing integrity, minimizing the risk of leaks in critical systems. - Long Lifespan
Made from durable materials, these gaskets have a prolonged operational life even in extreme environments. - Minimal Maintenance
Their robust design reduces maintenance requirements, leading to lower operational costs. - Environmental Safety
By preventing leaks of hazardous materials, RJGs contribute to environmental protection. - Customizability
Available in various shapes, sizes, and materials, RJGs can be tailored to specific industrial requirements.
How to Choose the Right Ring Joint Gasket?
Selecting the right RJG involves considering several factors:
• Operating Conditions: Evaluate the pressure, temperature, and type of media.
• Material Compatibility: Ensure the gasket material is compatible with the flange material and media.
• Flange Design: Choose the correct shape (oval or octagonal) based on the flange groove.
• Standards Compliance: Opt for gaskets adhering to industry standards like ASME B16.20.
Maintenance Tips for Optimal Performance
• Regularly inspect the gasket for signs of wear, deformation, or corrosion.
• Ensure the flange surfaces are clean and free of debris before installation.
• Use a torque wrench to apply uniform pressure during installation.
• Store gaskets in a dry and clean environment to prevent damage.
Conclusion
Ring Joint Gaskets are a cornerstone of industrial sealing technology, offering unparalleled performance in demanding applications. Whether in oil refineries or power plants, these gaskets ensure safe and efficient operations, making them a critical component in industrial infrastructure.
If you’re looking for high-quality Ring Joint Gaskets tailored to your specific needs, explore our comprehensive range at Rubber Seals and Gaskets. We offer premium sealing solutions designed to enhance the safety and efficiency of your operations.
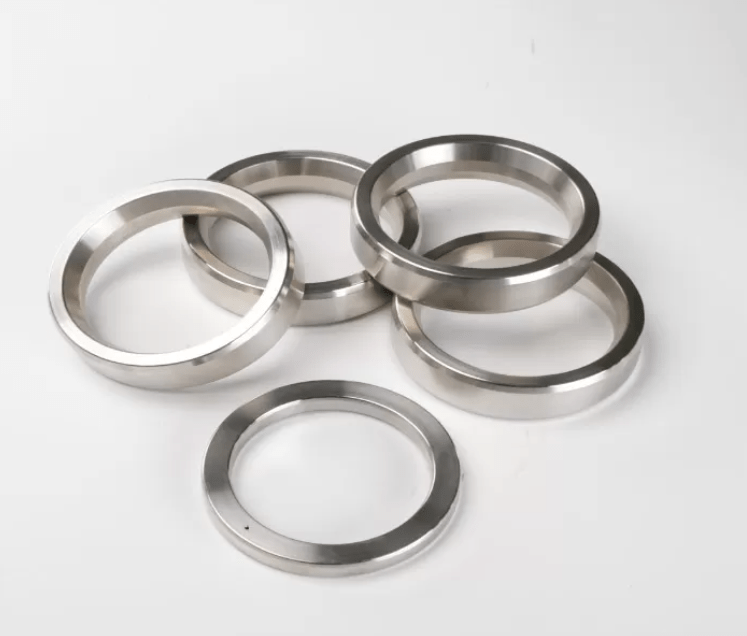
FAQs
In some cases, they can be reused after proper inspection, but it’s generally recommended to replace them for critical applications.
Yes, depending on the material, RJGs can resist corrosive media. Materials like Inconel and Hastelloy are ideal for such conditions.
RJGs are available in various standard sizes as per ASME B16.20, but custom sizes can also be manufactured.
The choice depends on the flange groove design. Consult the flange specifications or a sealing expert.
Ensure your industrial systems operate at peak performance with the right gasket solutions. Trust only the best with Rubber Seals and Gaskets!