BX and RX Ring Joint Gaskets: A Complete Guide
In high-pressure and high-temperature environments, the right sealing solution can make or break an operation. BX and RX Ring Joint Gaskets (RJGs) are specialized gaskets designed to handle these demanding conditions with precision and reliability. These gaskets are widely used in critical industries like oil and gas, petrochemicals, and power generation, where performance and safety are paramount.
In this blog, we’ll explore BX Ring Joint Gasket and RX Ring Joint Gaskets, diving into their unique features, applications, benefits, and the differences that set them apart.
What Are BX and RX Ring Joint Gaskets?
BX and RX gaskets are metallic sealing solutions used with RTJ (Ring Type Joint) flanges. These gaskets are designed to offer a tight, leak-proof seal under extreme conditions of pressure and temperature.
BX Ring Joint Gaskets
• Shape: BX gaskets are octagonal in shape and are designed for API 6BX flanges.
• Pressure Rating: Suitable for pressures up to 20,000 psi.
• Metal-to-Metal Sealing: Offers a true metal-to-metal seal, ensuring zero leakage in high-pressure applications.
RX Ring Joint Gaskets.
• Shape: RX gaskets are also octagonal but have a self-energizing feature.
• Pressure Rating: Used for pressures up to 15,000 psi.
• Sealing Mechanism: The self-energizing design improves sealing as pressure increases, making them ideal for dynamic conditions.
Both types are machined to exact specifications, ensuring precision and reliability in critical applications.
Key Features of BX and RX Ring Joint Gaskets
1. High Pressure Tolerance: BX gaskets excel in ultra-high-pressure systems, while RX gaskets are perfect for dynamic pressures.
2. Temperature Resistance: These gaskets can withstand extreme temperatures, making them suitable for industries like oil refining and power generation.
3. Durable Materials: Made from materials such as soft iron, stainless steel, Inconel, and other alloys to match application requirements.
4. Leak-Proof Performance: Designed for critical applications, these gaskets ensure zero leakage, even under fluctuating conditions.
5. Standards Compliance: BX and RX gaskets conform to API and ASME standards, ensuring compatibility and reliability.
Applications of BX and RX Ring Joint Gaskets
BX and RX gaskets are indispensable in various industries due to their robust sealing capabilities:
BX Gaskets
• Subsea Pipelines: Used in underwater pipelines where high pressure is a constant challenge.
• Blowout Preventers (BOPs): Essential in oil rigs to prevent uncontrolled well eruptions.
• Refineries: Handles high-pressure operations in hydrocarbon processing.
RX Gaskets
• Pipeline Valves: Ideal for dynamic pressure systems like pipeline valves and manifolds.
• Petrochemical Plants: Ensures safety in systems handling corrosive or volatile substances.
• Power Plants: Used in high-pressure steam and turbine systems.
BX vs. RX Ring Joint Gaskets: Key Differences
Aspect BX Gaskets RX Gaskets
Shape Octagonal Octagonal with self-energizing design
Pressure Range Up to 20,000 psi Up to 15,000 psi
Sealing Mechanism Metal-to-metal seal Self-energizing under pressure
Flange Compatibility API 6BX flanges API RTJ flanges
The choice between BX and RX gaskets depends on the operational requirements and flange design.
Advantages of BX and RX Ring Joint Gaskets
1. Exceptional Sealing Performance: Both BX and RX gaskets ensure zero leakage in critical systems.
2. Reliability in Extreme Conditions: Designed for high-pressure and high-temperature environments, they offer consistent performance.
3. Versatility: Available in various materials to match specific media and flange requirements.
4. Long Service Life: Their robust construction ensures durability, reducing replacement frequency.
5. Enhanced Safety: Prevents leaks of hazardous substances, safeguarding the environment and personnel.
Selecting the Right BX or RX Gasket
When choosing between BX and RX gaskets, consider the following factors:
• Flange Design: BX gaskets are specific to API 6BX flanges, while RX gaskets fit standard RTJ flanges.
• Operating Pressure: Choose BX for ultra-high-pressure systems and RX for dynamic conditions.
• Material Compatibility: Ensure the gasket material is compatible with the flange and media.
• Temperature Requirements: Match the material’s thermal resistance to the application needs.
Maintenance Tips for Optimal Performance
• Regularly inspect the gasket for signs of wear, deformation, or corrosion.
• Ensure the flange surfaces are clean and free of debris before installation.
• Use a torque wrench to apply uniform pressure during installation.
• Store gaskets in a dry and clean environment to prevent damage.
Maintenance and Installation Tips
1. Inspect Before Installation: Check the gasket and flange for any damage or irregularities.
2. Clean the Flange Groove: Remove debris or contaminants to ensure a proper seal.
3. Apply Uniform Pressure: Use a torque wrench to evenly tighten the bolts, preventing uneven stress.
4. Periodic Inspections: Regularly check gaskets in high-stress environments to ensure optimal performance.
Conclusion
BX and RX Ring Joint Gaskets are indispensable in industries where precision sealing is critical. Their ability to handle extreme pressures and temperatures makes them the go-to choice for oil and gas, petrochemicals, and other demanding sectors.
At Rubber Seals and Gaskets, we offer a wide range of BX and RX gaskets crafted to meet the highest standards of quality and performance. Whether you need a custom solution or a standard gasket, we’ve got you covered.
Explore our product range today and enhance the safety and efficiency of your operations with premium sealing solutions!
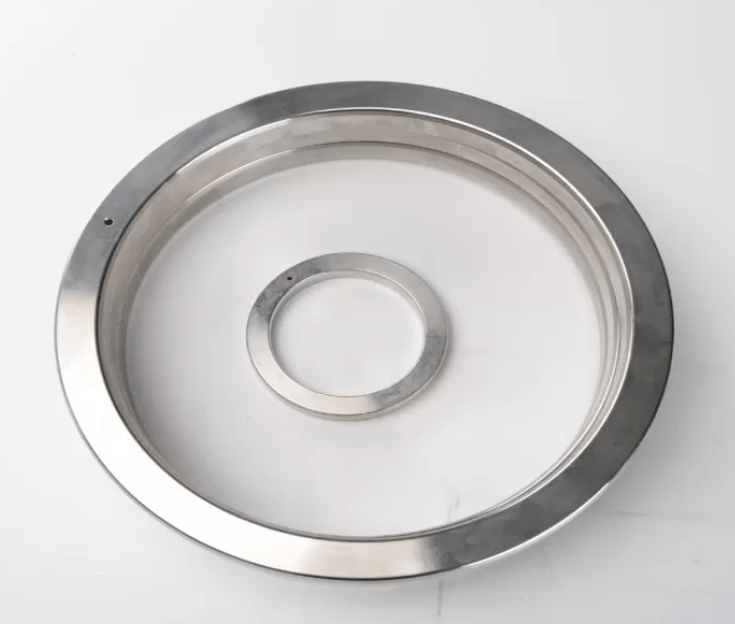
FAQs
Generally, these gaskets are not reused to ensure safety and sealing integrity in critical applications.
No, BX gaskets are specific to API 6BX flanges, while RX gaskets fit RTJ flanges.
Materials include soft iron, stainless steel, Inconel, and other alloys based on application requirements.
Follow flange specifications, use a torque wrench for uniform tightening, and ensure the groove is clean and debris-free.
Optimize your sealing systems with high-performance BX and RX gaskets from Rubber Seals and Gaskets!