Die Cut Gaskets: Precision Sealing Solutions for Every Industry
Die cut gaskets are a cornerstone of modern sealing solutions, offering unmatched precision and versatility. Designed for a wide range of applications, these gaskets are custom-made to meet the specific needs of industries such as automotive, aerospace, electronics, and manufacturing. At Rubber Seals and Gaskets, we pride ourselves on providing high-quality die cut gaskets tailored to your unique requirements.
This blog will delve into the features, advantages, applications, and materials of die cut gaskets, ensuring you have a comprehensive understanding of their value.
What Are Die Cut Gaskets?
Die cut gaskets are sealing components produced using a die cutting process, where a cutting tool, or die, is used to shape materials into precise designs. This method allows for the creation of gaskets with intricate shapes and tight tolerances, making them ideal for sealing applications that demand high accuracy.
Advantages of Die Cut Gaskets
Die cut gaskets offer several benefits that make them a preferred choice across industries:
1. Precision
Die cutting allows for exact replication of gasket designs, ensuring a perfect fit for your application.
2. Versatility
Available in various materials, shapes, and sizes, die cut gaskets can be customized for diverse applications.
3. Efficiency
The manufacturing process is quick and cost-effective, especially for high-volume production.
4. Consistency
Die cutting ensures uniformity in gasket production, maintaining consistent quality across batches.
5. Reduced Waste
Advanced die cutting techniques minimize material waste, contributing to cost savings and environmental sustainability.
Common Materials for Die Cut Gaskets
The material selection for die cut gaskets is crucial to their performance and durability. Some commonly used materials include:
1. Rubber
- Types: EPDM, Nitrile, Silicone, Neoprene
- Applications: Automotive, industrial, and outdoor environments
- Properties: Excellent flexibility, weather resistance, and sealing capability
2. Foam
- Types: Closed-cell foam, open-cell foam
- Applications: Electronics, HVAC systems
- Properties: Lightweight, compressible, and good thermal insulation
3. PTFE (Polytetrafluoroethylene)
- Applications: Chemical processing, food and beverage industries
- Properties: Chemical resistance, non-stick surface, and high-temperature tolerance
4. Cork
- Applications: Automotive, electrical equipment
- Properties: Resilient, oil-resistant, and eco-friendly
5. Metal
- Applications: High-pressure and high-temperature systems
- Properties: Robust, durable, and suitable for extreme conditions
6. Graphite
- Applications: Heat exchangers, boilers
- Properties: High-temperature resistance and excellent sealing under pressure
Applications of Die Cut Gaskets
Die cut gaskets are indispensable in various industries due to their adaptability and reliability.
1. Automotive Industry
- Used in engines, transmissions, and exhaust systems to provide leak-proof sealing.
2. Electronics
- Protect sensitive components from dust, moisture, and electromagnetic interference.
3. Aerospace
- Ensure reliability in high-performance applications, including fuel systems and airframes.
4. Medical Equipment
- Provide hygienic seals for medical devices and diagnostic equipment.
5. Industrial Machinery
- Prevent leakage in pumps, compressors, and heavy machinery.
6. Consumer Goods
- Used in household appliances for sealing and vibration dampening.
Why Choose Die Cut Gaskets for Your Needs?
Die cut gaskets are a versatile solution for industries requiring high-quality seals. Their ability to meet exact specifications ensures optimal performance in demanding environments. With advancements in die cutting technology, it’s easier than ever to produce gaskets that cater to complex designs and unique applications.
How to Choose the Right Die Cut Gasket?
When selecting a die cut gasket, consider the following factors:
1. Application Requirements
Identify the operating conditions, including temperature, pressure, and exposure to chemicals.
2. Material Compatibility
Choose a material that suits the specific requirements of your application.
3. Size and Design
Ensure the gasket matches the dimensions and shape of the sealing surface.
4. Performance Standards
Look for gaskets that meet industry certifications such as ASTM or ISO.
5. Manufacturer Expertise
Partner with a reputable supplier like Rubber Seals and Gaskets to ensure quality and reliability.
Die Cut Gaskets from Rubber Seals and Gaskets
At Rubber Seals and Gaskets, we specialize in creating high-quality die cut gaskets tailored to your unique requirements.
Our Offerings
- Custom Designs: Gaskets designed to fit your specific needs.
- Diverse Materials: Access to a wide range of materials, including rubber, foam, and PTFE.
- Expert Support: Guidance from experienced professionals to select the best gasket for your application.
- Consistent Quality: State-of-the-art manufacturing ensures precision and reliability.
Conclusion
Die cut gaskets are an essential component of modern sealing solutions, offering precision, versatility, and efficiency. Their adaptability across materials and applications makes them a valuable asset for industries worldwide.
If you’re in need of custom die cut gaskets, trust Rubber Seals and Gaskets to deliver products that meet your exact specifications. Contact us today to learn more about our offerings and discover how we can enhance your sealing solutions.
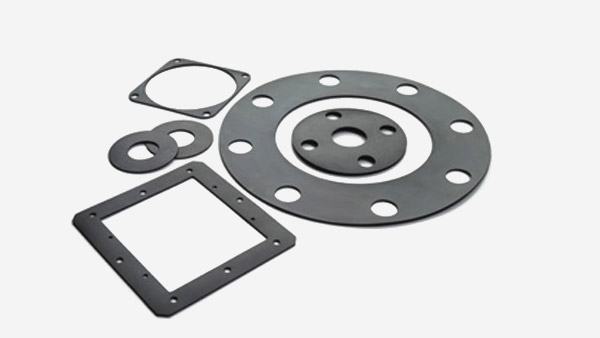
FAQs
Die cut gaskets are widely used in automotive, aerospace, electronics, medical equipment, and industrial applications.
Yes, they can be tailored to specific shapes, sizes, and materials to meet unique requirements.
They are created using a die cutting process that shapes materials into precise designs using specialized tools.
Invest in precision and reliability with die cut gaskets from Rubber Seals and Gaskets—your trusted partner for superior sealing solutions.