Hammer Union Seals: Essential Sealing Solutions for High-Pressure Applications
Introduction
Hammer union seals play a vital role in the oil and gas, chemical, and industrial sectors by ensuring leak-proof connections in high-pressure environments. These seals are specifically designed to withstand extreme pressure, temperature fluctuations, and aggressive chemicals, making them indispensable for various heavy-duty applications. In this article, we will explore the significance, applications, materials, and benefits of hammer union seals for rubber seals and gaskets.
What Are Hammer Union Seals?
Hammer union seals are specialized sealing components used in hammer unions, which are mechanical connectors employed in high-pressure piping systems. These seals prevent leakage and maintain system integrity, even under extreme operating conditions. They are typically made from elastomeric materials such as Nitrile (NBR), Hydrogenated Nitrile (HNBR), and Fluoroelastomers (FKM) to provide optimal resistance against pressure, heat, and corrosive substances.
Applications of Hammer Union Seals
Hammer union seals are widely used in industries where reliable sealing solutions are necessary for high-pressure operations. Some common applications include:
1. Oil and Gas Industry
Used in drilling rigs, wellhead equipment, and fracking systems.
Ensures leak-proof connections in pipelines carrying crude oil, natural gas, and drilling fluids.
2. Chemical Processing Plants
Provides resistance to harsh chemicals in fluid processing systems.
Prevents leaks in high-pressure reactors and transfer systems.
3. Hydraulic and Pneumatic Systems
Helps maintain pressure integrity in hydraulic power units.
Prevents air and fluid leaks in pneumatic transfer lines.
4. Industrial Equipment and Power Plants
Used in high-temperature steam and fluid transport systems.
Ensures safety and efficiency in energy generation processes.
Key Features and Benefits of Hammer Union Seals
– High-Pressure Resistance
Hammer union seals can withstand extreme pressure levels, making them ideal for applications that require reliable sealing under challenging conditions.
– Superior Chemical Compatibility
The choice of elastomer materials like FKM and HNBR ensures excellent resistance to aggressive chemicals, hydrocarbons, and corrosive fluids.
– Temperature Stability
These seals are designed to perform effectively in both high and low-temperature environments, ensuring durability across various industries.
– Enhanced Safety and Reliability
By preventing fluid leaks, hammer union seals contribute to workplace safety and reduce the risk of hazardous spills.
– Extended Service Life
Engineered for longevity, these seals minimize downtime and maintenance costs by providing long-lasting performance.
Choosing the Right Material for Hammer Union Seals
The performance of hammer union seals depends significantly on the material used. Below are some common elastomers and their properties:
Nitrile (NBR): Excellent resistance to oils, fuels, and moderate temperatures. Suitable for general industrial applications.
Hydrogenated Nitrile (HNBR): Enhanced temperature and chemical resistance, ideal for high-pressure and high-temperature applications.
Fluoroelastomer (FKM/Viton®): Superior resistance to extreme temperatures, aggressive chemicals, and petroleum-based fluids.
EPDM: Good resistance to heat, steam, and water-based applications but limited oil resistance.
Installation and Maintenance Tips
To maximize the efficiency of hammer union seals, proper installation and maintenance are essential. Here are some key tips:
Ensure Proper Fit: Use seals that match the exact size and pressure requirements of the hammer union connection.
Inspect Regularly: Periodic inspection of seals can help detect wear and tear early, preventing unexpected failures.
Use Compatible Lubricants: Avoid petroleum-based lubricants if they are not compatible with the seal material.
Replace When Necessary: Over time, seals may degrade due to pressure and chemical exposure. Replacing them at regular intervals ensures continued performance.
Conclusion
Hammer union seals are critical for maintaining leak-proof connections in high-pressure industrial applications. With a variety of materials available, selecting the right seal for your specific needs ensures maximum performance and durability.
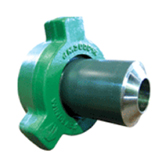
FAQs
Hammer union seals are used in high-pressure pipelines and connections to prevent leaks in industries such as oil and gas, chemical processing, and hydraulics.
The best material depends on the application. HNBR and FKM offer superior chemical and temperature resistance, while NBR is a cost-effective option for general use.
Replacement intervals vary based on operating conditions, but regular inspections can help determine when a seal needs to be replaced.
Yes, materials like FKM and HNBR are designed to perform in both high and low-temperature environments.
Looking for high-quality hammer union seals for your industrial applications? Contact us today to explore our range of premium sealing solutions tailored for maximum efficiency and durability!