Hydrogen Gaskets: A Comprehensive Guide for Rubber Seals and Gaskets
Hydrogen, as a highly flammable and lightweight gas, requires advanced sealing solutions to ensure safety and efficiency. In industrial applications involving hydrogen, the use of specialized gaskets, commonly referred to as hydrogen gaskets, plays a critical role in preventing leaks, withstanding extreme conditions, and ensuring the integrity of systems.
In this article, we explore the essential features, materials, applications, and benefits of hydrogen gaskets, emphasizing why they are indispensable in industries like energy, transportation, and chemical processing.
What Is a Hydrogen Gasket?
A hydrogen gasket is a sealing component specifically designed to handle the unique challenges posed by hydrogen gas. These gaskets ensure leak-proof seals in systems where hydrogen is stored, transported, or processed. Hydrogen gaskets are made from materials that resist gas permeation, endure extreme temperatures and pressures, and provide long-lasting performance in demanding environments.
Why Are Specialized Hydrogen Gaskets Necessary?
1. Hydrogen Permeability: Hydrogen is the smallest molecule, making it prone to leakage through microscopic gaps in standard sealing materials.
2. Extreme Operating Conditions: Hydrogen systems often operate under high pressures and varying temperatures, demanding robust gaskets that can maintain seals in such environments.
3. Safety Risks: Hydrogen is highly flammable, and leaks can lead to catastrophic consequences, making reliable sealing a non-negotiable requirement.
4. Corrosive Nature: Hydrogen can react with certain materials, causing degradation or embrittlement, requiring gaskets made from compatible, non-reactive materials.
Key Features of Hydrogen Gaskets
- Low Gas Permeability: Minimized hydrogen leakage through advanced material engineering.
- High Temperature Resistance: Capable of withstanding both cryogenic and elevated temperatures.
- Chemical Compatibility: Resistant to corrosion and chemical reactions with hydrogen.
- Durability: Engineered for long-term performance under continuous stress and environmental challenges.
- Customizable Design: Available in various shapes and sizes to suit different hydrogen systems.
Materials Used in Hydrogen Gaskets
1. PTFE (Polytetrafluoroethylene)
- High chemical resistance and low gas permeability.
- Suitable for cryogenic hydrogen applications.
2. Graphite
- Handles extreme temperatures and pressures.
- Often reinforced with metal cores for added strength.
3. Elastomers with Low Permeability
- Hydrogen-compatible rubbers like Viton® (FKM) and Nitrile (Buna-N) provide flexibility and durability.
4. Metallic Gaskets
- Spiral wound or ring joint gaskets made from stainless steel or Inconel® for high-pressure systems.
5. Hybrid Materials
- Composite gaskets combining metal and soft materials for optimal sealing performance in hydrogen systems.
Applications of Hydrogen Gaskets
Hydrogen gaskets are integral to industries that use hydrogen as a fuel, feedstock, or chemical.
1. Energy Sector
• Sealing components in hydrogen storage tanks, fuel cells, and electrolyzers for green energy production.
2. Automotive and Transportation
• Used in hydrogen-powered vehicles for leak-proof fuel delivery systems.
3. Chemical Processing
• Ensures safe handling of hydrogen in industrial chemical production.
4. Oil and Gas Industry
• Critical for hydrogen blending and refining processes.
5. Aerospace
• Hydrogen-powered propulsion systems and storage tanks require reliable gaskets.
Advantages of Using Hydrogen Gaskets
1. Enhanced Safety: Prevents hydrogen leaks, reducing the risk of accidents.
2. System Longevity: Resistant to wear, corrosion, and embrittlement.
3. Operational Efficiency: Maintains system integrity, minimizing downtime and maintenance costs.
4. Versatility: Compatible with a wide range of hydrogen-related applications and environments.
Choosing the Right Hydrogen Gasket
Selecting the correct hydrogen gasket involves evaluating several critical factors:
1. Operating Pressure and Temperature
o Ensure the gasket material can handle the system’s maximum pressure and temperature ranges.
2. Material Compatibility
o Choose materials that resist hydrogen permeation and chemical reactions.
3. Industry Standards
o Look for gaskets that meet industry certifications such as ISO, ASTM, or API.
4. Application-Specific Requirements
o Consider the unique demands of the hydrogen system, such as cryogenic capabilities or metal reinforcement.
Maintenance Tips for Hydrogen Gaskets
• Regular Inspection: Check for signs of wear, cracks, or degradation.
• Proper Installation: Use precise torque values to prevent over-compression or under-sealing.
• Surface Cleaning: Ensure mating surfaces are clean and free from debris.
• Timely Replacement: Replace gaskets at recommended intervals to maintain safety and efficiency.
Hydrogen Gaskets and the Future of Green Energy
As hydrogen emerges as a key player in renewable energy, the demand for specialized sealing solutions is expected to grow. Hydrogen gaskets are crucial for ensuring the safety and efficiency of systems in hydrogen production, storage, and transportation. Their role will only become more significant as industries worldwide transition toward cleaner energy solutions.
Why Choose Rubber Seals and Gaskets for Hydrogen Gaskets?
At Rubber Seals and Gaskets, we offer:
• Expertise in Material Selection: Our team helps you choose the ideal gasket material for hydrogen systems.
• Custom Gasket Solutions: We provide tailor-made gaskets for unique applications.
• High-Quality Standards: All products meet stringent industry certifications for safety and performance.
• Comprehensive Support: From design to delivery, we ensure your hydrogen sealing needs are met.
Conclusion
Hydrogen gaskets are indispensable for industries harnessing the power of hydrogen. With their exceptional sealing capabilities, durability, and safety features, they ensure leak-free operations in even the most challenging environments.
At Rubber Seals and Gaskets, we are committed to delivering top-tier hydrogen gasket solutions for diverse industrial applications. Contact us today to learn more about our products and services and how we can help you achieve a secure and efficient hydrogen system.
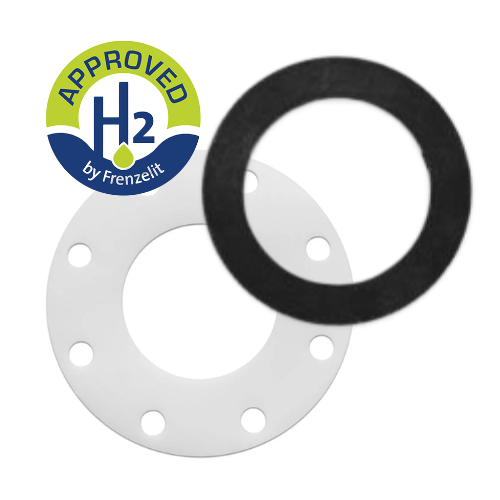
FAQs
Hydrogen gaskets are made from materials like PTFE, graphite, elastomers, or metallic composites to handle the unique challenges of hydrogen sealing.
Most hydrogen gaskets are designed for single-use to ensure safety and performance, although some metallic options may be reusable with proper inspection.
Yes, hydrogen gaskets are specifically engineered to withstand high-pressure environments, making them ideal for hydrogen applications.
Evaluate operating conditions, material compatibility, and industry standards to select the best gasket for your system.
Low permeability minimizes hydrogen leakage, ensuring safety and system integrity.
Seal your hydrogen systems with confidence—choose Rubber Seals and Gaskets for premium sealing solutions!