Inflatable Seals: Revolutionizing Sealing Solutions
Inflatable seals are a cutting-edge innovation in sealing technology, offering superior performance and versatility across various industries. Designed to create airtight and watertight seals, these seals adapt to changing environments and complex sealing requirements, making them indispensable in applications where traditional seals fall short.
In this blog, we’ll explore what inflatable seals are, their unique benefits, common applications, material options, and why they are the go-to choice for advanced sealing needs.
What Are Inflatable Seals?
An inflatable seal is a flexible and hollow seal made from elastomeric materials, designed to inflate and expand when pressurized. This controlled inflation ensures a tight seal against uneven surfaces, varying gaps, or irregular geometries. Inflatable seals are used in applications where traditional seals cannot achieve a sufficient or reliable seal due to the complexity of the sealing environment.
Key Features and Benefits of Inflatable Seals
1. Custom Fit for Complex Surfaces
• Inflatable seals can adapt to irregular shapes, making them ideal for sealing non-linear surfaces.
2. Superior Sealing Pressure
• Inflating the seal applies consistent pressure, creating an effective barrier against air, water, dust, or other substances.
3. Durability in Dynamic Environments
• These seals perform well under varying pressures, temperatures, and environmental conditions.
4. Reduced Maintenance
• Their adaptability minimizes wear and tear, extending service life and reducing the need for frequent replacements.
5. Ease of Operation
• Controlled inflation and deflation allow for seamless installation, removal, and operation, enhancing user convenience.
6. Enhanced Safety and Efficiency
• Provides reliable sealing for high-risk applications, such as hazardous chemical handling or sterile environments.
Common Applications of Inflatable Seals
Inflatable seals are versatile and are used in a wide array of industries and applications.
1. Pharmaceutical and Medical
• Sealing doors in clean rooms, autoclaves, and sterilizers.
• Ensuring contamination-free environments during sensitive processes.
2. Food and Beverage Processing
• Creating airtight seals in food processing equipment to maintain hygiene and quality.
3. Aerospace and Automotive
• Used in testing chambers, aerodynamic equipment, and vehicle assembly lines.
4. Marine and Shipbuilding
• Sealing hatches, watertight doors, and access panels in ships and submarines.
5. Nuclear and Chemical Industries
• Offering robust sealing solutions for equipment handling hazardous materials.
6. Industrial Machinery
• Used in large machinery where components need secure sealing under varying conditions.
Types of Inflatable Seals
Inflatable seals come in different configurations to cater to specific needs.
1. Straight Seals
• Commonly used in linear applications like sliding doors and equipment panels.
2. Curved Seals
• Designed for circular or irregular sealing surfaces, such as hatches and lids.
3. Custom Shapes
• Fully tailored seals for unique or non-standard applications.
4. Single-Acting vs. Double-Acting Seals
• Single-acting seals inflate in one direction, while double-acting seals offer sealing in multiple directions for added versatility.
Material Options for Inflatable Seals
The choice of material is critical in ensuring optimal performance and durability of inflatable seals.
1. EPDM (Ethylene Propylene Diene Monomer)
• Excellent resistance to UV, ozone, and weathering.
• Suitable for outdoor and water-based applications.
2. Silicone
• Handles extreme temperatures (-60°C to 200°C) and offers a smooth surface for hygienic applications.
• Ideal for food, medical, and pharmaceutical industries.
3. Neoprene
• Resistant to oils, greases, and moderate chemicals.
• Frequently used in industrial and automotive settings.
4. Viton® (FKM)
• Exceptional chemical resistance and high-temperature stability.
• Perfect for nuclear, chemical, and aerospace applications.
5. Nitrile (Buna-N)
• Resistant to oils and hydrocarbons.
• Suitable for sealing applications involving fuel or oil exposure.
Factors to Consider When Choosing Inflatable Seals
1. Application Environment
• Assess the temperature, pressure, and chemical exposure conditions.
2. Material Compatibility
• Select a material that is resistant to the substances or environments it will encounter.
3. Inflation Requirements
• Determine the pressure range and type of inflation mechanism needed.
4. Size and Shape
• Ensure the seal fits the specific dimensions and configurations of your application.
5. Compliance Standards
• For specialized industries like food or medical, choose seals that meet FDA or other regulatory standards.
Maintenance Tips for Inflatable Seals
1. Regular Inspection: Periodically check for signs of wear, cracks, or leaks.
2. Proper Cleaning: Use appropriate cleaning solutions to maintain material integrity.
3. Pressure Management: Avoid over-inflation to prevent damage.
4. Correct Installation: Ensure the seal is properly aligned during installation.
5. Timely Replacement: Replace damaged or aged seals to maintain optimal performance.
Why Choose Rubber Seals and Gaskets for Inflatable Seals?
At Rubber Seals and Gaskets, we pride ourselves on delivering top-quality inflatable seals for diverse applications. Here’s what sets us apart:
• Tailored Solutions: Custom designs to meet your exact specifications.
• Premium Materials: Durable, high-performance seals crafted from industry-approved materials.
• Expert Guidance: Professional advice on selecting and maintaining the right seal for your needs.
• Unmatched Quality: Rigorous quality control to ensure reliable performance in all conditions.
Conclusion
Inflatable seals are a game-changer in sealing technology, offering unparalleled adaptability and performance for complex applications. Their ability to provide airtight and watertight seals, combined with their versatility and durability, makes them an invaluable asset across industries.
Whether you’re looking to enhance operational efficiency, ensure safety, or meet industry standards, Rubber Seals and Gaskets has the perfect inflatable seal for you. Contact us today to discover how our innovative solutions can meet your sealing needs.
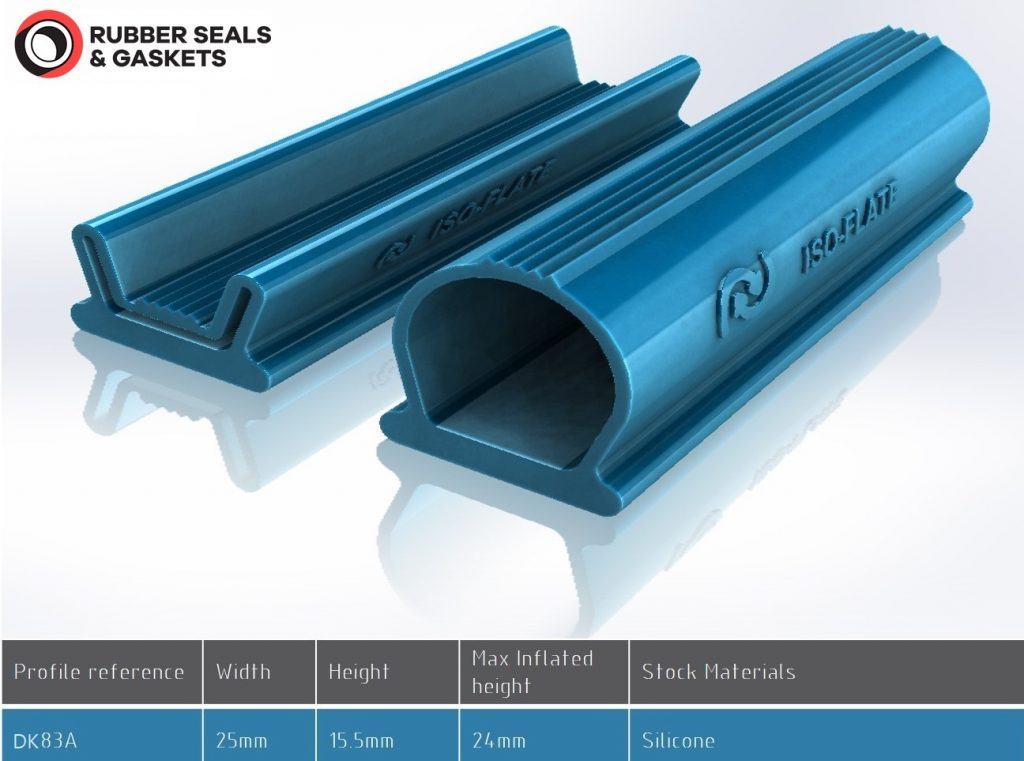
FAQs
Inflatable seals are used for applications requiring a tight and adaptable seal, such as cleanrooms, machinery, and hatches.
Yes, seals made from materials like silicone and Viton® can withstand extreme temperatures.
Consider factors like application environment, material compatibility, and size requirements.
Yes, with proper maintenance, inflatable seals can be reused multiple times.
Experience the future of sealing with Rubber Seals and Gaskets—your trusted partner for advanced sealing solutions!