Manifold Valves: Essential Components for Fluid Control in Rubber Seals and Gaskets
Manifold valves are crucial components in various industrial applications, providing efficient fluid control in systems requiring precise pressure and flow regulation. These valves are commonly used in rubber seals and gaskets applications, ensuring leak-proof performance, durability, and enhanced operational efficiency. In this blog, we will explore manifold valves, their types, applications, advantages, and why they are vital for industries relying on rubber sealing solutions.
What Are Manifold Valves?
Manifold valves are multi-port valves designed to streamline piping systems by consolidating multiple control valves into a single unit. These valves play a critical role in regulating pressure, isolating instruments, and ensuring smooth operation in hydraulic and pneumatic systems. In applications involving rubber seals and gaskets, manifold valves help maintain a leak-proof and efficient system, reducing maintenance requirements and operational downtime.
Types of Manifold Valves
Manifold valves come in various configurations, each designed for specific industrial applications. The most common types include:
1. 2-Valve Manifold
Used for pressure gauges and static pressure transmitters.
Consists of an isolation valve and a vent valve.
Helps in accurate pressure measurement and system calibration.
2. 3-Valve Manifold
Typically used in differential pressure transmitters.
Comprises two isolation valves and one equalizing valve.
Allows for safe and efficient pressure balancing in measuring instruments.
3. 5-Valve Manifold
Suitable for complex measurement applications.
Contains two isolation valves, an equalizing valve, and two vent/test valves.
Enhances accuracy and safety in high-pressure environments.
4. Block and Bleed Manifold
Used for isolating instrumentation from the main system.
Consists of a block valve and a bleed valve to remove excess pressure.
Prevents system contamination and ensures safety during maintenance.
Applications of Manifold Valves in Rubber Seals and Gaskets
Manifold valves are integral to industries that rely on rubber seals and gaskets for sealing solutions. Some key applications include:
Oil and Gas Industry: Used in pressure measurement systems to ensure leak-free operations.
Chemical Processing: Helps in controlling the flow of aggressive chemicals while preventing leaks in rubber-sealed systems.
Pharmaceuticals: Ensures precise fluid control and contamination-free processing.
Hydraulic and Pneumatic Systems: Provides secure connections and pressure management in systems using rubber gaskets.
Food and Beverage Industry: Maintains hygiene and efficiency in food processing systems with sealing requirements.
Benefits of Using Manifold Valves
Manifold valves offer several advantages that make them indispensable in fluid control applications, particularly those involving rubber seals and gaskets:
Enhanced Efficiency: Reduces the need for multiple separate valves, optimizing system design.
Leak Prevention: Ensures secure connections and minimizes the risk of fluid leaks.
Space-Saving Design: Consolidates multiple valve functions into a single compact unit.
Reduced Maintenance: Minimizes wear and tear on sealing components, extending system life.
Improved Safety: Isolates hazardous fluids and maintains system integrity during maintenance operations.
Cost-Effective: Reduces installation and operational costs by simplifying piping configurations.
How to Select the Right Manifold Valve
Choosing the appropriate manifold valve depends on several factors:
Operating Pressure: Ensure the valve can withstand the pressure requirements of your application.
Material Compatibility: Select materials like stainless steel, brass, or specialized coatings based on fluid type.
Number of Ports: Determine the required number of connections for your system.
Temperature Range: Verify the valve’s capability to handle the working temperature of the application.
Seal Compatibility: Ensure that the valve seals are suitable for use with rubber gaskets and other sealing components.
Maintenance Tips for Manifold Valves
To maximize the performance and lifespan of manifold valves, follow these maintenance guidelines:
Regular Inspections: Check for signs of wear, corrosion, or leakage.
Lubrication: Apply suitable lubricants to moving parts to ensure smooth operation.
Seal Replacement: Replace rubber gaskets and seals periodically to prevent system failures.
Proper Installation: Ensure correct mounting and alignment to avoid stress on valve connections.
Cleanliness: Keep the valve and surrounding area clean to prevent contamination and clogging.
Conclusion
Manifold valves are essential for industries relying on rubber seals and gaskets, offering enhanced efficiency, leak prevention, and system safety. Selecting the right manifold valve tailored to your specific needs can improve operational performance and reduce maintenance costs. If you’re looking for high-quality manifold valves and sealing solutions, contact us today to find the best products for your application!
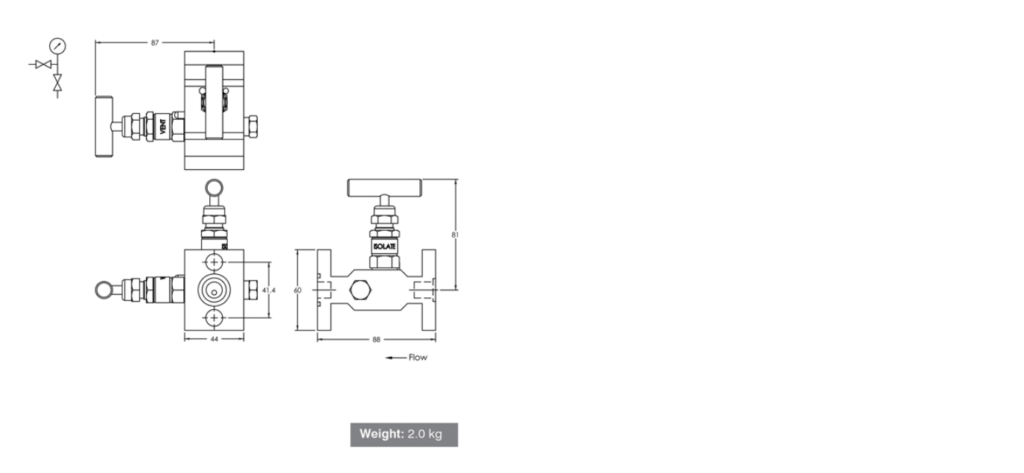
FAQs
A manifold valve consolidates multiple control valves into a single unit, enabling precise fluid control, pressure regulation, and system isolation.
Yes, manifold valves are designed to handle high-pressure environments, especially in hydraulic and pneumatic systems.
Manifold valves ensure tight sealing, reducing the risk of fluid leaks by integrating high-quality rubber gaskets and precision-engineered connections.
Stainless steel, brass, and specialized alloys are the most common materials used, chosen based on the specific application requirements.
Routine inspections should be conducted at least once every six months, with maintenance schedules based on system usage and environmental conditions.
Looking for reliable manifold valves and rubber sealing solutions? Get in touch with us today to explore our range of high-performance manifold valves designed for various industrial applications. Contact us now!