Medical Seals
Rubber sealing for medical applications requires high precision as well meeting industry regulations. Diyak Rubber molding capabilities meet highest industry precision from molding custom designed parts and seals to microminiature solutions. Our custom molding capabilities is a complement to our vast inventory and capabilities to produce o-rings in various sizes, durometers and materials from medical grade materials.
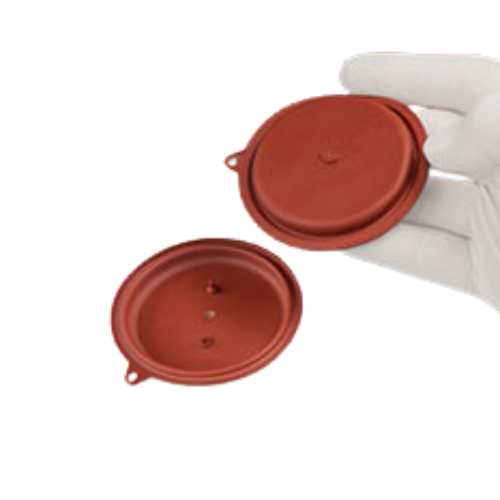
Medical Grade Elastomers
Medical grade rubbers are a group of compounds that are typically tested to FDA USP Class VI or ISO 10993 test protocols. It is important to note that “FDA Rubber” is typically considered in the rubber industry as food contact rubber that complies with FDA 21 CFR 177.2600. This specifies the ingredients that can be used in a rubber formulation and extraction testing in water and oil.
Diyak Rubber’s medical grade elastomers feature improved chemical resistance, excellent heat resistance and low permeability to gas.
Medical Grade Silicone
When properly prepared, the benefits include fulfillment of USP Class VI and ISO 10993 requirements, and can be sterilized with autoclave, gamma, ETO. Less than 30 day implant and long-term implant grades available. Medical grade pigments are also available.
Limitations: Generally, low abrasion and tear resistance, and high friction characteristics preclude silicones from effectively sealing some dynamic applications. Silicones are also highly permeable to gases and are generally not recommended for exposure to ketones (MEK, acetone) or concentrated acids.
Ethylene-Propylene
- Trade Names
- Vistalon — Exxon Mobil
- Nordel — Dow Chemical
- Kaltan — Arlanxeo
- Royalene — Lion Elastomer
- ASTM D1418 Designation
- EPDM
- ASTM D2000/SAE J200 Type, Class
- AA, BA, CA, DA
- Diyak Compound Designation
- EP
- Standard Color
- Black
- Description
- A copolymer of ethylene and propylene (EPR), combined with a third comonomer diene (EPDM), Ethylene Propylene has gained wide seal industry acceptance for its excellent ozone and chemical resistance characteristics.
- Key Uses
- Outdoor weather resistant uses, automotive brake systems, automobile cooling systems, low torque drive belts, watertight applications with low water permeability.
- Temperature Range
- Standard Compound: -76°F to +275°F
- Special Compound: -76°F to 302°F
- Hardness (Shore A)
- 40 to 95
- Features
- When compounded using peroxide curing agents, high temperature service can reach +350°F. Good resistance to acids and solvents (i.e. MEK and Acetone).
- Limitations
- Have no resistance to hydrocarbon fluids.
Fluorocarbon (Viton)
Trade Name
- Viton™ — Chemours Company
- Dyneon — 3M Company
- DAI-EL — Daikin
- Technoflow — Solvay
- ASTM D1418 Designation
- FKM
- ASTM D2000/SAE Type, Class
- HK
- Diyak Compound Designation
- VT
- Standard Color
- Black
- Description
- Combining high temperature resistance with outstanding chemical resistance, Fluorocarbon-based compounds approach the ideal for a universal o-ring material.
- Key Uses
- Seals for aircraft engines. Seals for automotive fuel handling systems. High temperature/low compression set applications. Wide chemical exposure situations. Low outgassing makes excellent vacuum seals.
- Temperature Range
- Standard Compound: -13°F to +446°F
- Special Compounds: -40°F to +446°F
- Hardness (Shore A)
- 45 to 90
- Features
- High fluorine grades offer higher resistance to swell in high octane and oxygenated fuel blends. This gives superior performance in Ethanol/Methanol blended gasoline. Also, Fluorocarbon offers improved resistance to steam for higher temperature services. Low temperature bases can improve performance to -40°F. New polymers being offered have improved chemical resistance and low temperature performance.
- Viton™ Extreme™ ETP offers similar chemical compatibility as FFKM with temperature resistance to +446°F.
- Special compounds, using new polymer technologies, provide improved low temperature performance with a TR(10) of -40°F and brittleness to -76°F.
- Limitations
- Fluorocarbons are not recommended for exposure to ketones, amines, low molecular weight esters and ethers, nitro hydrocarbons, hot hydrofluoric or chlorosulfonic acids, or Skydrol® fluids. They are also not recommended for situations requiring good low temperature flexibility.
Medical Parts and Seals
From simple seals to the most complex parts, DiyakRubber utilizes a host of sophisticated technologies and processes, including LSR capabilities and a Class 10000 ISO-07 Clean Room to consistently manufacture the high quality components you demand directly in our USA plant.
- Seals for medical appliances
- Ventilators
- O-Rings for medical testing consumables
- Medical pump seals
- IV components
- Feeding devices
- Implant materials
- USP Class VI and ISO 10993 materials available