Non-Asbestos Gaskets: A Modern Sealing Solution for Industrial Applications
Gaskets are critical components in industries that rely on secure and leak-proof sealing solutions. While asbestos gaskets were widely used in the past for their excellent heat resistance and durability, the health risks associated with asbestos have led to the rise of safer alternatives. Non-asbestos gaskets are now the preferred choice for industrial sealing, offering outstanding performance without compromising health or safety.
In this article, we’ll explore the benefits, types, materials, and applications of non-asbestos gaskets, making them a sustainable choice for industries.
What Are Non-Asbestos Gaskets?
Non-asbestos gaskets are sealing components made from synthetic fibers, rubber, or other non-toxic materials instead of asbestos. These gaskets provide the same durability, heat resistance, and sealing efficiency as their asbestos-based counterparts, without posing health hazards.
They are widely used in industries like automotive, chemical, oil & gas, and manufacturing, where safety, efficiency, and reliability are paramount.
Benefits of Non-Asbestos Gaskets
1. Health and Safety
Non-asbestos gaskets eliminate the health risks associated with asbestos exposure, ensuring a safer working environment.
2. Environmental Sustainability
These gaskets are eco-friendly, reducing the environmental impact of industrial operations.
3. High Performance
They offer excellent resistance to heat, chemicals, and pressure, making them suitable for demanding applications.
4. Cost-Effectiveness
Non-asbestos gaskets are a cost-efficient alternative to other high-performance sealing materials.
5. Versatility
Available in various materials and configurations, they can be customized for specific industrial needs.
Types of Non-Asbestos Gaskets
1. Compressed Non-Asbestos Gaskets (CNAF)
- Made by compressing fibers, rubber, and fillers.
- Ideal for applications involving steam, oil, and chemicals.
2. Graphite-Based Gaskets
- Contain graphite for enhanced heat and pressure resistance.
- Commonly used in high-temperature environments.
3. PTFE-Based Gaskets
- Made from polytetrafluoroethylene (PTFE), offering excellent chemical resistance.
- Suitable for aggressive chemical environments.
4. Elastomer-Based Gaskets
- Composed of rubber materials like EPDM or Nitrile.
- Provide flexibility and resistance to weather and mild chemicals.
Materials Used in Non-Asbestos Gaskets
Non-asbestos gaskets are crafted from a variety of materials to cater to different industrial requirements:
1. Aramid Fiber
- High strength and excellent thermal stability.
- Commonly used in compressed non-asbestos gaskets.
2. Graphite
- Exceptional heat resistance and chemical stability.
- Ideal for high-temperature and pressure applications.
3. PTFE (Polytetrafluoroethylene)
- Non-reactive and highly resistant to chemicals.
- Suitable for applications involving aggressive media.
4. Rubber
- Offers flexibility and resilience.
- Used in applications requiring dynamic sealing.
Applications of Non-Asbestos Gaskets
Non-asbestos gaskets are used in a wide range of industries:
1. Automotive Industry
- Used in engines, exhaust systems, and fuel systems for leak-proof sealing.
2. Oil & Gas
- Provide reliable sealing in pipelines, valves, and high-pressure systems.
3. Chemical Processing
- Resistant to aggressive chemicals, making them ideal for storage tanks and reactors.
4. Power Plants
- Handle high-temperature and high-pressure environments effectively.
5. Food and Beverage
- Food-grade non-asbestos gaskets ensure hygienic sealing in processing equipment.
6. Pharmaceuticals
- Used in sterile environments to prevent contamination.
How to Choose the Right Non-Asbestos Gasket
Selecting the right gasket depends on several factors:
Application Environment
- Consider the temperature, pressure, and type of media (gas, liquid, or chemical).
Material Compatibility
- Ensure the gasket material is compatible with the media it will be in contact with.
Size and Shape
- Gaskets must fit precisely to avoid leaks or performance issues.
Certifications
- Look for certifications like FDA approval for food-grade applications or ASTM standards for industrial use.
Maintenance Tips for Non-Asbestos Gaskets
Regular Inspection
- Check for wear, cracks, or deformation to avoid unexpected failures.
Proper Installation
- Use the correct tools and follow manufacturer guidelines for installation.
Timely Replacement
- Replace gaskets at regular intervals or during routine maintenance to ensure system reliability.
Storage
- Store gaskets in a cool, dry place to prevent material degradation
Why Choose Rubber Seals and Gaskets for Non-Asbestos Gaskets?
At Rubber Seals and Gaskets, we specialize in providing high-quality non-asbestos gaskets tailored to diverse industrial needs.
Why Partner with Us?
- Premium Materials: Only the best fibers, rubbers, and fillers.
- Custom Solutions: Gaskets designed to meet your specific requirements.
- Competitive Pricing: Affordable without compromising quality.
- Expert Support: Guidance to help you select the perfect gasket for your application.
Conclusion
Non-asbestos gaskets are a safe, sustainable, and high-performing solution for industrial sealing. They combine the benefits of asbestos-free materials with excellent durability, chemical resistance, and versatility, making them indispensable across industries.
For premium non-asbestos gaskets and expert advice, trust Rubber Seals and Gaskets to deliver unmatched quality and service. Contact us today to learn more about our range of gaskets and sealing solutions.
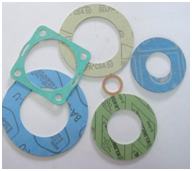
FAQs
Non-asbestos gaskets provide excellent sealing performance without the health hazards associated with asbestos.
Yes, materials like graphite and aramid fiber make them ideal for high-temperature environments.
Consider the application environment, material compatibility, and required certifications.
For all your sealing needs, explore the comprehensive range of non-asbestos gaskets at Rubber Seals and Gaskets!