Pneumatic Seals: Essential Components for Efficient Air and Gas Systems
Introduction
Pneumatic seals play a critical role in ensuring the efficiency and reliability of air and gas-based systems. These seals are designed to prevent leakage, enhance system performance, and extend the life of pneumatic components. Whether used in industrial machinery, automotive applications, or automation systems, high-quality pneumatic seals are essential for maintaining optimal functionality.
What Are Pneumatic Seals?
Pneumatic seals are specialized sealing components designed for use in systems that operate with compressed air or gas. Unlike hydraulic seals that work with liquid-based systems, pneumatic seals handle lower pressure levels and must withstand rapid movement and dry-running conditions.
Types of Pneumatic Seals
Rod Seals – Prevent leakage in reciprocating rods, ensuring smooth motion in pneumatic cylinders.
Piston Seals – Provide a tight seal between the piston and cylinder wall to prevent air leakage and maintain pressure.
Wiper Seals (Dust Seals) – Keep contaminants such as dust and dirt out of the system, improving the longevity of components.
O-Rings and X-Rings – Commonly used in static and dynamic applications for sealing joints and preventing air loss.
Cushion Seals – Absorb energy and reduce impact at the end of piston strokes.
Wear Rings – Help guide pistons and rods, reducing friction and wear.
Key Benefits of Pneumatic Seals
Leak Prevention: Ensures efficient sealing, preventing loss of compressed air.
High-Speed Performance: Designed to handle rapid cycling and high-speed motion without compromising efficiency.
Low Friction: Provides smooth operation and reduces energy consumption.
Durability: Made from materials resistant to wear, chemicals, and temperature variations.
Extended Service Life: Reduces maintenance frequency and operational downtime.
Materials Used in Pneumatic Seals
The choice of material impacts the performance and longevity of pneumatic seals. Some commonly used materials include:
Nitrile Rubber (NBR): Excellent resistance to wear and oil, suitable for standard pneumatic applications.
Polyurethane (PU): High durability, flexibility, and resistance to abrasion.
Fluorocarbon (FKM/Viton): Superior chemical and heat resistance for demanding applications.
Silicone (VMQ): Used in applications requiring high-temperature resistance and flexibility.
PTFE (Teflon): Provides low friction and chemical resistance, often used in high-speed applications.
Applications of Pneumatic Seals
Pneumatic seals are widely used across various industries, including:
Automotive Industry: Used in braking systems, suspension systems, and actuators.
Industrial Machinery: Essential in pneumatic cylinders, valves, and air compressors.
Aerospace Sector: Used in aircraft actuators and air control systems.
Medical Equipment: Ensures precision and reliability in medical devices and tools.
Food Processing: Meets hygiene standards while maintaining airtight seals in food-grade machinery.
Choosing the Right Pneumatic Seal
When selecting a pneumatic seal, consider the following factors:
Operating Pressure and Speed: Choose a seal that can withstand the required pressure range and motion speed.
Temperature Compatibility: Ensure the material can endure temperature variations within the system.
Chemical Resistance: Select a seal that can resist exposure to oils, gases, and other chemicals.
Environmental Conditions: Consider factors like humidity, dust, and contaminants..
Conclusion
Pneumatic seals are vital for ensuring the smooth and efficient operation of air and gas-based systems. Selecting the right seal type, material, and design enhances performance, reduces maintenance, and extends the life of pneumatic components. Whether for industrial automation, automotive applications, or medical equipment, high-quality pneumatic seals are indispensable for leak-free and efficient operation.
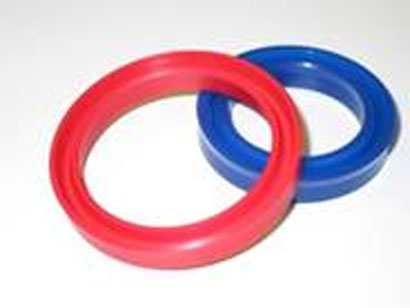
FAQs
Pneumatic seals are designed for air or gas systems, typically operating at lower pressures, while hydraulic seals are used in liquid-based systems with higher pressure levels.
The replacement frequency depends on the operating conditions, material, and application. Regular inspections and preventive maintenance can help extend their lifespan.
Yes, certain materials like PTFE, FKM, and silicone offer high-temperature resistance and can function effectively in extreme environments.
Seal failure can result from excessive friction, contamination, improper installation, or material degradation due to temperature or chemical exposure.
You can source premium-quality pneumatic seals from reputable suppliers like Rubber Seals and Gaskets, ensuring durability and reliability for your applications.
For premium-quality pneumatic seals and other sealing solutions, explore our extensive range at Rubber Seals and Gaskets. Contact us today for expert guidance, custom sealing solutions, and competitive pricing!