Rubber Extrusions: Essential Components for Rubber Seals and Gaskets
Introduction
Rubber extrusions play a crucial role in various sealing applications, offering durability, flexibility, and resistance to environmental conditions. Used in industries ranging from automotive to construction, these components ensure effective sealing, shock absorption, and vibration resistance. In this article, we will explore the benefits, types, applications, and considerations for selecting rubber extrusions for different industrial needs.
What are Rubber Extrusions?
Rubber extrusions are continuous rubber profiles created through an extrusion process, where uncured rubber is forced through a shaped die to form specific cross-sectional shapes. These extrusions are then vulcanized to achieve the desired strength and elasticity. They are widely used for sealing, weatherproofing, insulation, and noise reduction in industrial and commercial applications.
Benefits of Rubber Extrusions
Highly Flexible & Durable – Rubber extrusions maintain their shape and function even under constant stress and exposure.
Weather & Chemical Resistance – Many rubber materials offer excellent resistance to harsh weather, chemicals, and UV exposure.
Customizable Shapes & Sizes – Available in various profiles such as D-seals, P-strips, U-channels, and more to fit specific applications.
Excellent Sealing Properties – Effectively blocks air, dust, moisture, and noise for improved performance.
Cost-Effective & Long-Lasting – Reduces maintenance costs by providing reliable performance over time.
Common Types of Rubber Extrusions
EPDM Rubber Extrusions
Excellent weather, ozone, and UV resistance
Ideal for outdoor applications like window and door seals
Common in automotive and construction industries
Silicone Rubber Extrusions
High-temperature resistance and flexibility
FDA-approved variants available for food and medical applications
Offers excellent electrical insulation
Neoprene Rubber Extrusions
Good resistance to oils, chemicals, and abrasion
Used in marine and industrial applications
Provides strong sealing against moisture and gases
Nitrile Rubber Extrusions
High resistance to fuel, oil, and petroleum-based fluids
Common in automotive and aerospace industries
Durable and flexible under extreme conditions
Natural Rubber Extrusions
High elasticity and excellent mechanical properties
Suitable for dynamic sealing applications
Used in vibration-damping and shock-absorbing systems
Applications of Rubber Extrusions
Automotive Industry – Used in weatherstripping, door seals, window gaskets, and engine bay seals.
Construction & Building – Applied in door frames, window seals, expansion joints, and waterproofing solutions.
Industrial Machinery – Ensures vibration damping, sealing, and protective insulation in heavy machinery.
Aerospace & Marine – Provides high-performance sealing against extreme temperatures and moisture.
Medical & Food Industry – Silicone rubber extrusions are widely used in sterile and FDA-compliant environments.
How to Choose the Right Rubber Extrusion?
When selecting rubber extrusions, consider the following factors:
Material Compatibility – Choose a rubber type that suits the operating environment (e.g., high-temperature, chemical exposure).
Profile & Shape – Select the right cross-sectional shape for effective sealing and fitting.
Hardness & Flexibility – Ensure the material has the right balance of rigidity and elasticity for the application.
Resistance Requirements – Determine the need for resistance to UV rays, ozone, chemicals, oils, or heat.
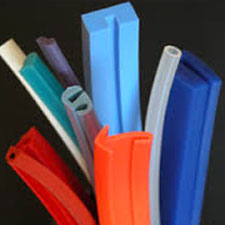
FAQs
Rubber extrusions are used for sealing, weatherproofing, insulation, and vibration reduction in various industries.
EPDM and silicone are the best choices for outdoor applications due to their superior weather and UV resistance.
Yes, rubber extrusions can be custom-designed to meet specific industrial requirements.
At Rubber Seals and Gaskets, we offer a wide range of custom and standard rubber extrusions designed to meet your industrial needs. Contact us today to find the perfect sealing solution!