Spiral Wound Metal Gaskets: The Ultimate Sealing Solution
In industrial operations, sealing efficiency is critical to ensuring safety, reliability, and operational efficiency. Spiral Wound Metal Gaskets (SWMGs) have emerged as a trusted solution for challenging sealing applications. Known for their versatility and durability, these gaskets are extensively used in industries such as oil and gas, power generation, petrochemicals, and more.
In this article, we’ll explore what Spiral Wound Metal Gaskets are, their design, materials, benefits, and the applications where they shine.
What Are Spiral Wound Metal Gaskets?
Spiral Wound Metal Gaskets are multi-layered gaskets designed to provide a reliable seal under extreme pressure and temperature conditions. They consist of alternating layers of metal and filler material, which are wound in a spiral form. This unique construction allows the gasket to accommodate flange surface irregularities and thermal expansion while maintaining a tight seal.
Key Components of SWMGs:
1. Metal Windings: Typically made from stainless steel, Inconel, or other alloys, providing strength and flexibility.
2. Filler Material: Non-metallic materials like graphite, PTFE, or mica, chosen for their sealing properties and compatibility with the media.
3. Inner and Outer Rings (optional): Enhances the gasket’s structural integrity and ensures proper alignment during installation.
Advantages of Spiral Wound Metal Gaskets
1. Exceptional Sealing Capability: SWMGs can handle a wide range of pressures and temperatures, making them ideal for demanding environments.
2. Resilience to Flange Imperfections: The flexible construction accommodates surface irregularities, ensuring a leak-proof seal.
3. Thermal and Mechanical Flexibility: The layered design allows the gasket to expand and contract with thermal changes, maintaining its seal.
4. Versatility: Available in various material combinations to suit different media and environmental conditions.
5. Standards Compliance: SWMGs adhere to industry standards like ASME, API, and EN, ensuring reliability and compatibility.
Materials Used in Spiral Wound Metal Gaskets
Metal Windings
• Stainless Steel: Corrosion-resistant and suitable for high-pressure applications.
• Inconel: Ideal for extreme temperatures and aggressive chemical environments.
• Monel: Excellent for marine and saltwater applications.
• Hastelloy: Best for highly corrosive media.
Filler Materials
• Graphite: Handles high temperatures and resists chemical attack.
• PTFE: Offers excellent chemical resistance for aggressive media.
• Mica: Suitable for high-temperature, non-oxidizing environments.
The choice of materials depends on factors like temperature, pressure, and chemical compatibility.
Applications of Spiral Wound Metal Gaskets
Thanks to their versatility, SWMGs are used across numerous industries:
1. Oil and Gas
- Sealing pipelines, valves, and pressure vessels.
- Preventing leaks in high-pressure hydrocarbon systems.
2. Power Generation
- Used in boilers, heat exchangers, and steam turbines.
3. Petrochemical Industry
- Ensuring safe operation in reactors and chemical processing units.
4. Pharmaceuticals
- Suitable for sterile environments requiring chemical-resistant sealing solutions.
5. Aerospace
- Ideal for systems requiring reliability under high thermal and mechanical stress.
6. Marine Applications
- Effective in sealing components exposed to saltwater environments.
Types of Spiral Wound Metal Gaskets
1. Basic Type (Style R)
No rings; used in tongue-and-groove or male-female flanges.
2. With Inner Ring (Style RIR)
Inner ring prevents over-compression and adds stability.
3. With Outer Ring (Style CG)
Outer ring aids in gasket centering and provides additional radial strength.
4. With Inner and Outer Rings (Style CGI)
Combines the benefits of both rings, ideal for high-pressure, high-temperature applications.
Why Choose Spiral Wound Metal Gaskets?
1. High Performance: These gaskets offer unmatched sealing efficiency in demanding conditions.
2. Customizability: Available in various shapes, sizes, and material combinations to meet specific needs.
3. Longevity: Durable design ensures extended service life, reducing replacement frequency.
4. Cost-Effective: By preventing leaks and minimizing downtime, SWMGs save costs in the long run.
5. Environmental Protection: Helps prevent the escape of hazardous or toxic substances, ensuring safety and compliance.
How to Install Spiral Wound Metal Gaskets
1. Inspect the Flange Surface
Ensure it is clean, flat, and free of debris.
2. Align the Gasket
If the gasket has a centering ring, ensure proper alignment with the flange bolts.
3. Tighten Bolts Evenly
Use a torque wrench to apply uniform pressure across all bolts, avoiding uneven compression.
4. Perform a Leak Test
Verify the seal by performing a pressure or vacuum test before starting operations.
Maintenance Tips
• Regularly inspect gaskets in critical applications for signs of wear or damage.
• Store gaskets in a dry, clean environment to prevent contamination.
• Replace gaskets during routine maintenance to ensure continued reliability.
Conclusion
Spiral Wound Metal Gaskets are the backbone of sealing technology in high-pressure and high-temperature environments. Their robust design, exceptional performance, and adaptability make them indispensable in industries that prioritize safety and efficiency.
At Rubber Seals and Gaskets, we provide premium-quality Spiral Wound Metal Gaskets tailored to your specific requirements. Whether you need a standard or custom solution, our products are designed to meet the highest industry standards.
Explore our comprehensive range of gaskets today and ensure your operations run smoothly and safely.
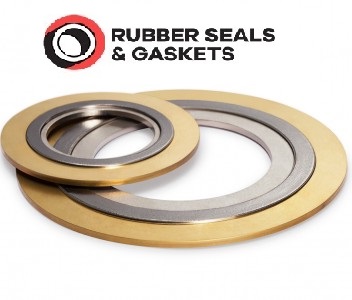
FAQs
Industries like oil and gas, power generation, petrochemicals, and pharmaceuticals widely use SWMGs for critical sealing applications.
While reusing gaskets is possible in some cases, it is generally recommended to replace them for optimal performance and safety.
Inner rings prevent over-compression, while outer rings help with alignment and add structural stability.
Yes, with appropriate material selection, SWMGs can handle highly corrosive environments.
Ensure your industrial systems operate with the highest efficiency by investing in the best sealing solutions from Rubber Seals and Gaskets!